-
生成品に、変質や雑菌の汚染が生じている
洗浄性を悪化させる微細な凹凸の存在 -
配管の一部にサビが浮いたり腐食が見られる
管内部を保護する酸化皮膜の組成の乱れや劣化 -
タンク内に赤い汚れ(ルージュ)が現れ、生成品に影響している
加工時の残留物等が影響した経時的な変質・腐食 -
高純度ガスが金属イオンで汚染されている
配管内部の表面処理が不十分でイオンが発生
プロセス配管の金属表面は常にストレスにさらされ、以下のような問題に直面します。
半導体製造業
不要イオンの混入で歩留まりが悪化
半導体チップの高性能化はとどまるところを知りません。そのため回路はより微細になり製造の難度が上がるばかり。同時に、歩留まりの悪化も許されません。
半導体製造には不活性ガスや、材料ガス等に高純度ガスが用いられます。これらにほんの僅かのメタルイオン汚染があると、半導体チップの性能や生産性は大きな影響を被ることになります。
PPTクラスの純度が求められる高純度ガスの供給ラインや充填ラインなどタンクや配管などでは、金属イオン溶出によるコンタミネーション阻止は重要課題です。
ポイント
不動態膜の厚み不足や金属組成の僅かな乱れ、酸化物や洗浄剤の残存などによるトラブルの潜在化を排除するため、電解研磨後、不動態膜の強化処理をお奨めします。

医薬品製造業
ルージュの発生による品質変化
医薬・食品製造では、特に純水系を使用するサニタリー管ラインにおいてルージュの発生が問題となります。不動態化処理されているステンレス配管でも、徐々に配管内部に赤い※錆びが浮き立ち、その様子からこれをルージュと呼びます。
配管表面が劣化・腐食している場所や溶接部などに多く、非常に高温になりやすい場所に生じバリデーション対応などに大きな課題となります。
※ルージュはその組成により、赤・オレンジ系、黒・灰色系、褐色系など多様な発色をする。不活性なものも存在するが、時間をおいて活性化することがあるの注意が必要。
ポイント
ルージュの原因は、バフ粉油分の残留、鋭敏な条痕など加工時の影響にある。さらに、これらを除去する仕上げ研磨や洗浄などが不十分な状態では、電解研磨をかけてもルージュの原因を内在化させてしまう。

食品加工業
雑菌の増殖による食品汚染
食品の炭水化物・タンパク質・脂肪などが機械に付着し変性物になります。それが食品に混入したり微生物の温床となるため、食品機械は、①付着や液溜まりしにくく②洗浄と殺菌・消毒が容易な「サニタリー構造」とされています。
しかし、特に配管内の溶接部は、合わせ精度、溶接部の仕上がり、溶接後の研磨や表面処理が不完全だと洗浄できない場所が生じます。洗浄が不完全だと、後に行う消毒処理の効果も不十分になる場合が多いと言われています。結果として、生物的危害要因(Hazard)※である微生物やその生成毒などが残留し、食製品の品質に影響が出始めます。
※HACCP(Hazard Analysis and Critical Control Point:ハサップ)食品等事業者自らが食中毒菌汚染や異物混入等の危害要因(ハザード)を把握した上で、原材料の入荷から製品の出荷に至る全工程の中で、それらの危害要因を除去又は低減させるために特に重要な工程を管理し、製品の安全性を確保しようとする衛生管理の手法(厚生労働省ホームページより)
ポイント
不適切な加工材料選定、平均粗さが規格範囲外、粒度の乱れた研磨、機械加工でできる微細空洞の放置、部分溶接、粗い裏波、不適切な内角溶接などに注意。

一般・共通
孔食やすきま腐食による設備の短命化
表面処理されたステンレスの配管であっても、直管・継手の防食皮膜に局部腐食を生じさせる孔食やすきま腐食などに要注意です。塩化物イオンを扱う、あるいは触れる環境では、高耐食性のステンレスであっても、金属加工や表面処理の品質によって腐食の進行に大きな差を生じます。
溶接などの残留応力の影響で応力腐食割れなどが発生し、生産設備の寿命を縮めます。こうした表面劣化の進行は重大損傷になる前においても、生成品の品質に徐々に影響を大きくしていきます。
ポイント
不均質な不動態皮膜の形成、事前に十分な前洗浄が行われず表面が汚染されている。仕上げ洗浄後にも酸化物や電解液成分が金属表面に残留する。

金属の表面に問題がありそうだと思ったら「日章アステックの表面処理ソリューション」
-
プロセス配管やタンクの表面処理は当社の専門分野です
-
表面処理効果を最大限に引き出す加工提案ができます
-
表面処理鋼管(EP/BA)の在庫販売もできます。(在庫量は国内トップクラス)
-
ベトナム現地法人でも製薬クラスの加工と電解研磨が可能です
日章アステックがご用意した表面処理ソリューション
※写真はイメージであり、実際の製品やサービスと異なる場合があります
もっと詳しく知りたい方はこちら 表面処理の各メニューをご紹介します
機械的研磨 ーバフ研磨・バイブレーション研磨
機械的に金属表面の凹凸を除去する。
機械的に金属表面上の凹凸を削り飛ばし平坦面を作ります。バフ研磨は使用する研磨剤の粒度や機械特性、あるいは職人の練度によって仕上がりは変わってきます。

留意点
-
形状的には鏡面のような光沢面にできる。組成的には加工熱などの影響で安定した状態とは言えない。
-
形状的:バフ研磨では、機械的に表面の凹凸を潰していく。そのため目視レベルでは美しい光沢面も、ミクロレベルでは空洞や条痕の谷間が存在。その隙間に金属粉や研磨剤、油分等が潜伏し残留している。
-
組成的:溶接やバフ研磨の加工熱で、表層部は金属の組織や結晶構造が変化し活性(変化しやすい)状態にある。
ポイント
電解研磨等後処理を意識したハイグレードな長尺パイプの精密研磨(VI NA ASTEC)。サニタリーパイプに残る縦方向の条痕も目立たなくなるほど、パイプ内はハイグレードな仕上がりに。電解研磨の効果を一層高め浄化性が増します。
詳細情報
電解研磨 (EP:Electro Polishing)
電解作用で金属面のミクロな凹凸を溶かし平坦化・均質化
電解作用によって金属表面の凸部を溶解し金属表面の形状を平坦化します。その過程で表面(1~3nm)に不動態化膜とクロム集約によるクロムリッチな層が形成。耐食性の大幅向上に寄与します。
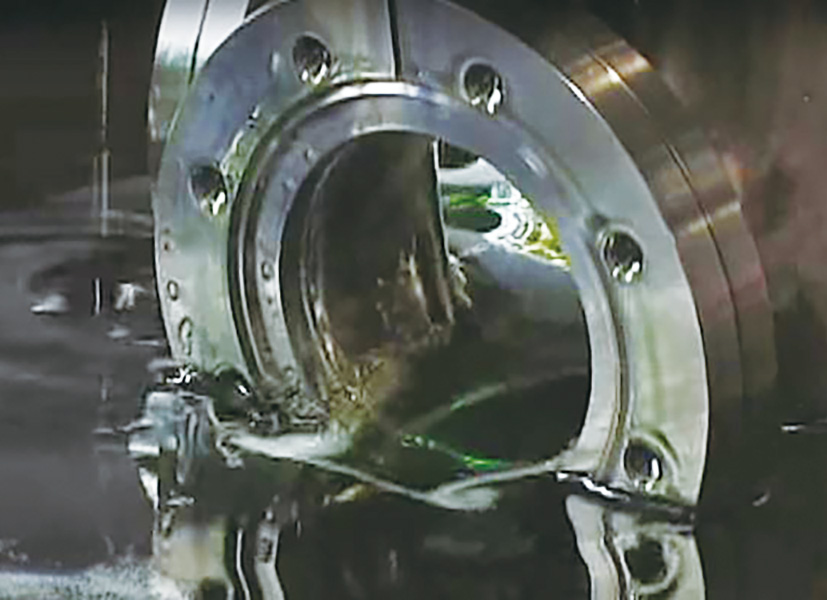
留意点
-
電解研磨による溶解は、金属表面のミクロ的な電解反応であり、大きな条痕などは解消できない。平坦度を上げるには事前に制度の高い機械研磨を行う必要がある。EPは、雑なバフ研磨を補うものではない。
-
電解反応時に表面の汚染物をある程度除去できる。しかし金属面や汚染物の状況によっては汚染物除去という目的では電解研磨は十分ではない場合もある。
-
組成的:溶接やバフ研磨の加工熱で、金属の組織や結晶構造が変化し活性(変化しやすい)状態にある。
ポイント
金属溶出による汚染を嫌う場合は、不動態膜を強化した後述のGold EP(GEP)/Gold EP White(GEPW)を強く推奨する。
詳細情報
Gold EP (GEP) / Gold EP White (GEPW)
厚く均質な酸化皮膜の形成による表面保護と金属溶出の抑制
電解研磨によって形成された不動態膜は平坦で均質だが、その厚みは1~3nmで決して厚くはありません。また局所的には結晶の乱れを潜在させている可能性もあります。Gold EP(GEP)/Gold EP White(GEPW)は、EP後に更に一定時間熱処理を加え、表面に厚い酸化皮膜を成長させています。
GEP/GEPWは、金属溶イオン溶出が極めて低レベルに抑えられるため、高純度ガスラインなどに用いられます。またわずかに金属表面に残留する有機物も、熱処理の過程で減少するのでクリーンです。
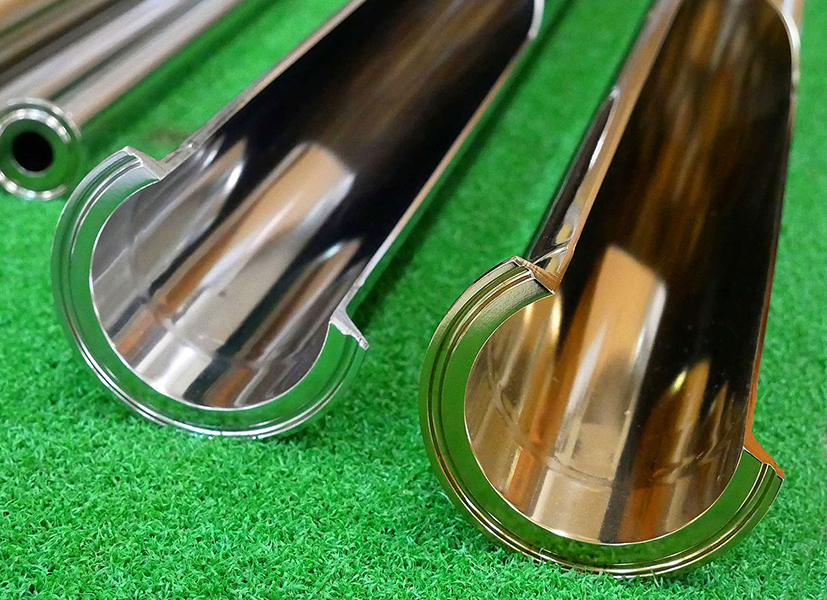
ポイント
-
GEPは、EP後の表面上にクロム酸化膜と鉄酸化膜を成長させ、その厚みはEP時の約10倍になる。
-
GEPWは、GEPを化学処理し表層の鉄酸化膜を溶解したもの。クロム酸化膜はEP時の約3倍
詳細情報
脱脂洗浄 ーアルカリ脱脂洗浄(浸漬法)
付着した油分を中心に金属表面に汚れを除去する
加工後の金属表面には様々な付着物(金属粉・マシン油・バフ粉・金属スマットなど)が固着しています。アルカリ脱脂洗浄は、アルカリ薬剤のけん化作用や界面活性剤の働きでこれら汚染物を溶かし浮かし剥ぎ取ります。
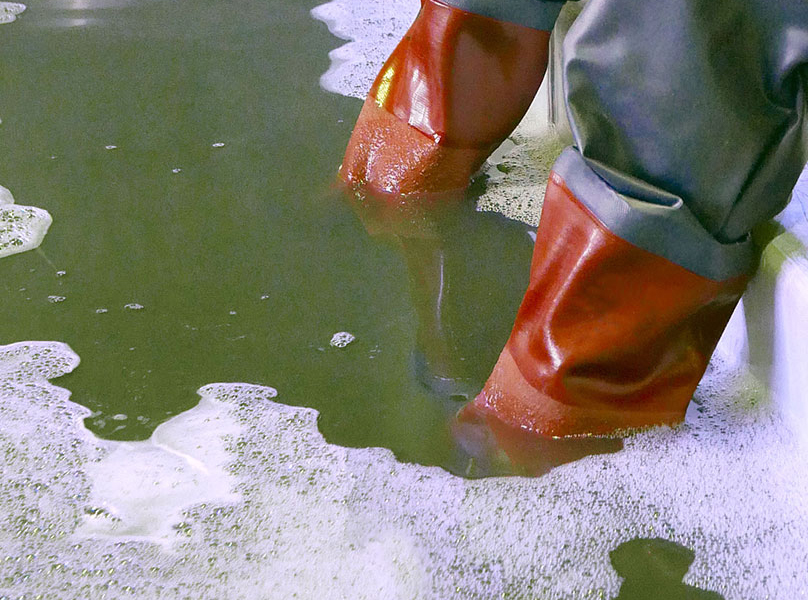
留意点
-
アルカリ薬剤への浸漬では、金属表面の全ての凹凸部に薬剤を浸透・接触させることは不可能で、汚れの除去には限界がある。
-
アルカリ脱脂後に不動態化処理を行っても、バフや溶接による構造的・組成的な不均質をすべて解消することは難しい。より良好な表面を作るには、電解研磨で凸部を溶解し均質な不動態膜を作ることが望ましい。
詳細情報
電解研磨の後処理 ーアルカリ脱脂と弱酸洗浄
電解処理の酸化物などを中心に除去し表面を整える
電解研磨処理によって溶け出した酸化物や電解液などの付着物を除去します。アルカリ処理は加温や濃度によって脱脂効果が変化します。金属表面を溶解し表面に食い込んだ汚れも浮かせて除去します。
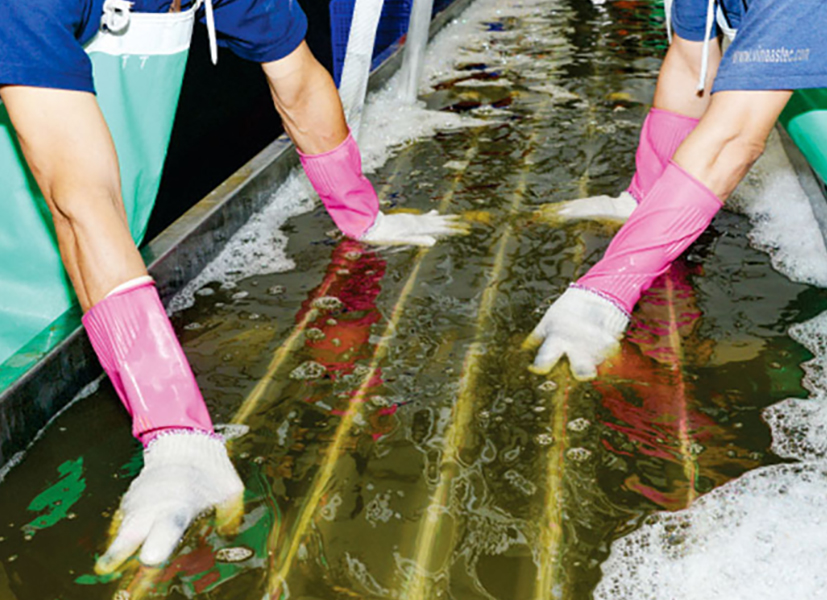
留意点
-
アルカリ処理は金属表面の溶解を伴うので、後処理として弱酸による中和や不動態膜の再生をおこなう。
詳細情報
酸洗(酸洗い)/ 錆落とし
溶接加工などによるスケールや汚れ、もらいサビなどを除去
酸洗(酸洗い)は、溶接後のビードスケールや酸化膜スケールを除去するために用います。また、同時に細かいバリや油分やその他の汚れも除去します。酸洗により、ステンレスの不動態膜も除去されてしまいますが、酸洗後すぐに再生されます。

留意点
-
酸洗には、硫酸や塩酸を用いるので、その保管、扱い、残液や洗浄液の処理、有毒ガスに注意する必要がある。
-
酸洗を仕上げとして用いる場合、金属表面は梨地になり平滑性は高くない。
詳細情報
※鉄製品の錆落としは当社(国内)では承っておりません。
超純水による精密洗浄 / レギューラー洗浄
電解研磨や化学洗浄の後に必要なクリーン洗浄
電解研磨 / GEP / GEPWなどの表面処理工程では、アルカリや酸などへの浸漬洗浄に加え、超純水※1による高圧洗浄※2を行います。超純水は各種のイオンを含まないため、それらによる汚染なしに付着するパーティクルなどを除去できます。

※1超純水:超純水メーカー保証値: 17.5MΩ・cm(出口保証値)
※2高圧洗浄:6MPa/約60℃
ポイント
-
水はモノを溶かしやすく水道水には、カルシウム、マグネシウム、塩化物などのイオンが含まれている。洗浄時にこれら不要イオンが製品を汚染しないように、高度な洗浄性を求められる製品では超純水による洗浄を行う。
ピュアスチーム(PS)洗浄
高温水蒸気によるタンクや容器内面の超クリーン洗浄
ピュアスチーム(PS)洗浄浄)では、ピュアウォータ(当社はRO水)の熱水蒸気をタンクや容器に一定時間満たし、汚れを浮かしとります。熱水蒸気が液体の水では表面張力で入り込めないような微細部にも到達し汚れを落とすとともに除菌効果も期待できます。
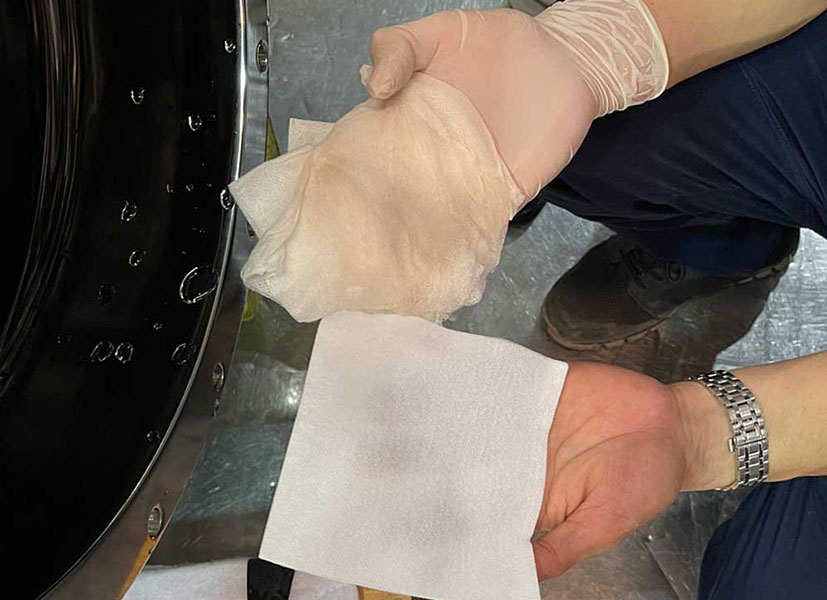
ポイント
-
ピュアスチーム洗浄は、当社ではベトナム現地法人VINA ASTECで対応。
詳細情報
クリーンエア乾燥 / 窒素ブロー
残留する水分や細かい異物を乾燥または吹き飛ばす
クリーンエアまたは窒素ガスでブローします。エアは中空糸フィルタ( 0.01μm濾過)でクリーン化しています。熱乾燥炉(0.3μm HEPAフィルタ付)では、乾燥温度60℃で30分以上乾燥します。
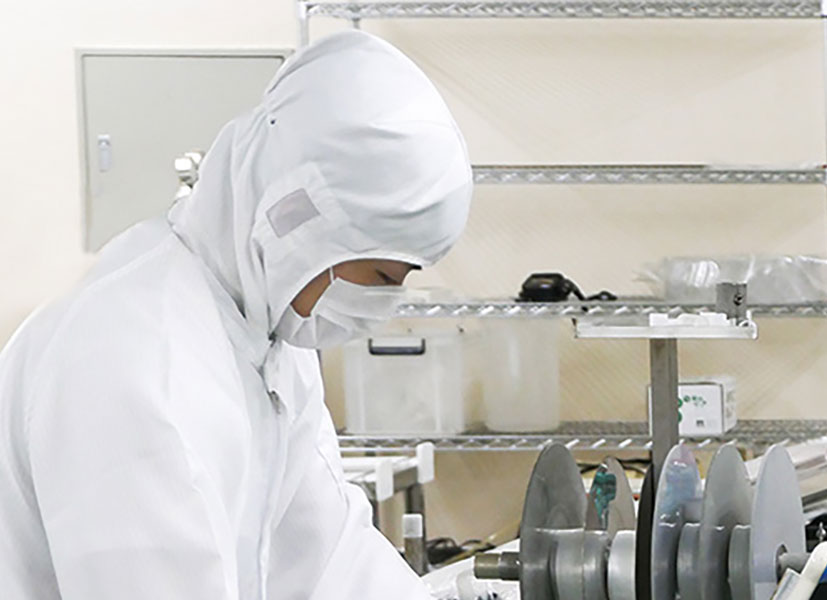
ポイント
-
最終検査と包装は、パーティクルが除去されたクリーンルーム(JIS B9920 Class 6)で行う。
-
窒素ブローは、静電気の発生や酸化を防ぎたい場合に用いる。
詳細情報